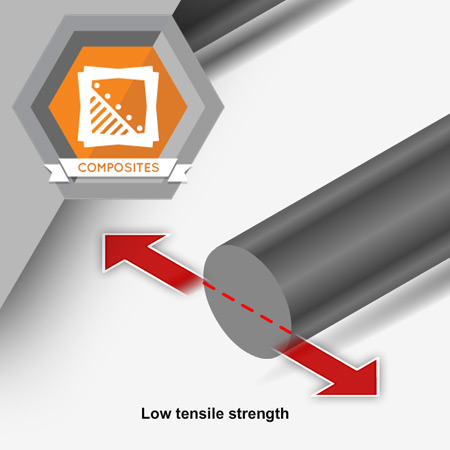
A composite part increases its strength by adding plies with fibers at different orientations. Engineers use computers and software to design composite parts and determine the number and orientations of each ply so that the finished composite part will be strong enough to withstand expected and unexpected loads in the final product.
Estimated completion time (hours): 0.9
Objectives
By the end of this course, you will be able to do the following:
- Define the differences between a balanced and unbalanced layup
- Understand the effects both balanced and unbalanced layups have on the finished composite part’s strength
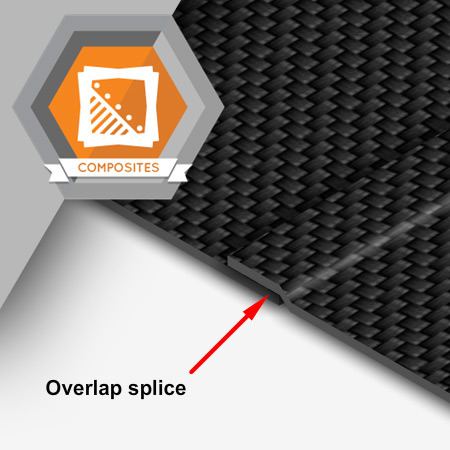
In very large or complex composite parts, it is often necessary to make a complete ply layer out of two or more pieces of material. When two or more pieces are used to form a ply layer, the pieces must be positioned so that they will bond together during curing to form a continuous layer in the finished part. The area where these pieces are joined together is called a splice.
Estimated completion time (hours): 0.8
Objectives
By the end of this course, you will be able to do the following:
- Define and identify the use of a butt splice
- Define and identify the use of an overlap splice
- List common requirements of a butt splice
- List common requirements of an overlap splice
- List common requirements for staggering splices
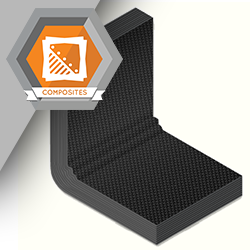
In composite manufacturing, a wrinkle is an area of a ply that does not lay flat and smooth. The plies overlap, buckle, or fold back on themselves. A gap is an unintended separation between the fibers in a ply.
Estimated completion time (hours): 0.7
Objectives
By the end of this course, you will be able to do the following:
- Define wrinkle
- Define gap
- Describe the consequences of wrinkles and gaps
- List ways to prevent wrinkles and gaps
- Describe how to use the splice table on an engineering drawing
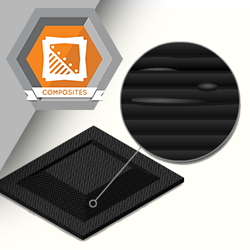
In composite manufacturing, a void is an area of unintended separation between the layers of the finished composite part. Voids are also called pockets.
Estimated completion time (hours): 0.7
Objectives
By the end of this course, you will be able to do the following:
- Define void
- Define porosity
- List the causes of voids and porosity
- Describe the consequences of a void or porosity
- List ways that voids and porosity can be prevented
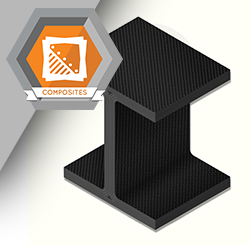
Radius filler is fiber material used to fill a void in the laid-up composite part. The process for creating radius filler has four steps.
Estimated completion time (hours): 0.7
Objectives
By the end of this course, you will be able to do the following:
- Define radius filler
- Describe the process for creating radius filler
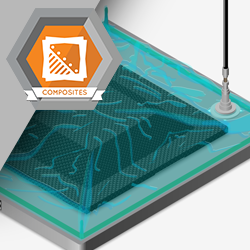
A poorly bagged part can impact the success of the curing cycle. A bag that leaks will not maintain a vacuum and the part will not be compacted as needed. A bag that is not pleated properly might rupture during the curing cycle. Improper bagging techniques can lead to defects in the part, with the end result that the part is not acceptable and must be scrapped.
Objective
By the end of this course, you will be able to do the following:
-
Describe the techniques for bagging and curing three dimensional assemblies
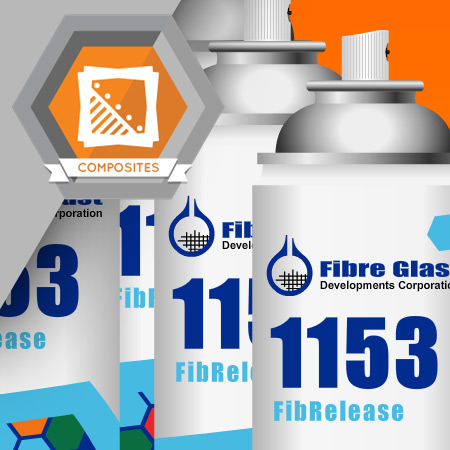
Lay-up and bagging is a process for creating composite components. To perform lay-up and bagging tasks, you need to know how to use specialized equipment and materials.
Estimated completion time (hours): 1.4
Objectives
By the end this course, you will be able to
- Identify the equipment and materials used in bagging and laying up composite components
- Identify the purpose of each piece of equipment
- Understand the role of the equipment in the bagging and lay-up process
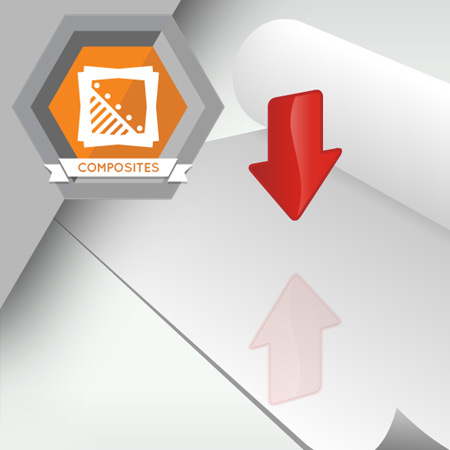
Lay-up is the process for layering the composite materials when constructing a composite component. Understanding the purpose of each lay-up type is essential to your success in composite manufacturing. The type of lay-up will determine the structural properties of the composite component.
Estimated completion time (hours): 1.1
Objectives
By the end of this course, you will be able to do the following:
- Identify the documentation used in laying up composite components
- Identify material orientation used in laying up composite components
- Understand the purpose of material orientation used in composite lay-up
- Identify different lay-up types

A cure cycle controller is a computer system that controls the heating elements, heating blankets, and other accessories used for curing composite structures.
Estimated completion time (hours): 1.0
Objectives
By the end of this course, you will be able to do the following:
- Define cure cycle controller
- List the components of a hot bonder
- Describe how a hot bonder is programmed
- Describe the proper care and storage of a hot bonder
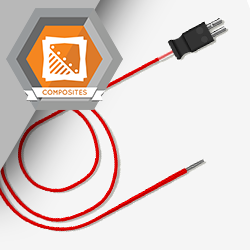
A thermocouple is a sensor used to measure the temperature of the composite part during the curing cycle.
Estimated completion time (hours): 0.7
Objectives
By the end of this course, you will be able to do the following:
- Describe thermo-management in composite manufacturing
- Understand the proper placement and number of thermocouples required for proper thermo-management of the part during the cure process
- Explain the basic science of exothermic reactions and their relation to part geometry and thickness